前言
前期小编跟大家分享过寄售模式下收入确认的时点问题,里面所讲的寄售模式其实是VMI(供应商管理库存)三种运作模式中的一种,即“供应商-制造商”运作模式。该模式作为一种创新型库存管理方法,其高度集成的精益供应链管理思想,打破了传统各自为政的库存管理格局。因此,零售业、制造业领域具有规模的企业自然的成为VMI模式的粉丝。富士康作为全球3C领域的代工之王,也是国内最早实行VMI的企业之一,该模式在富士康已实行多年,其成效如何,是否真的实现了高度集成的精益管理格局?小编将在下文中揭晓答案。
什么是VMI
VMI概念的提出最早在上世纪80年代,是在共同的框架协议下,由供应商来管理库存,使得供应链系统同步运行并持续改进的合作性策略,也是一种基于供应链环境下的库存管理模式。VMI库存管理模式有三个方面的特点:一是信息共享,供应链环境下节点企业间的信息开放,供应商通过信息共享、及时沟通来进行资源的合理配置;二是供应商拥有库存的所有权,使用后付款;三是需求准确预测。VMI模式下,供需双方从传统的博弈关系转变成为策略联盟的关系。理论上来说,VMI高度集成的精益供💛应链管理思想能够有效降低供应链总成本,抑制牛鞭效应,实现供需双方共赢等目标。
VIM的实施主🐻要由供应链上的核心企业来推动。基于核心企业所处供应链位置的不同,VMI主要有三种运作模式:供应商-制造商(核心企业)、供应商-零售商(核心企业)、制造商(核心企业)-分销商或零售商。富士康实行的VMI就属于供应商-制造商(核心企业)的运作模式。
富士康的库存管理
富士康主要生产3C电子产品,其库存主要包括原物料,在产品、产成品三大类。一般情况下,除了客户资金突然出现💫异常或产品出现质量问题,成品最💙多在成品仓存放一周,而在产品都流通于各业务单元的生产线上,所以原物料库存自然而然的成为富士康重点管控对象。
富士康现行的原物料管理方法主要为传统的ABC分类管理法,即按照库存的种类与库存占用资金金额的大小,将原物料划分为A、B、C三类进行分级管理。富士康则从实际出发设立了自己的四级库存分类原则以制定相应管理策略,依据库存分类原则及管理策略,目前富士康的原物料库存🎐主要来源于正式订单、VMI、JIT三种模式。
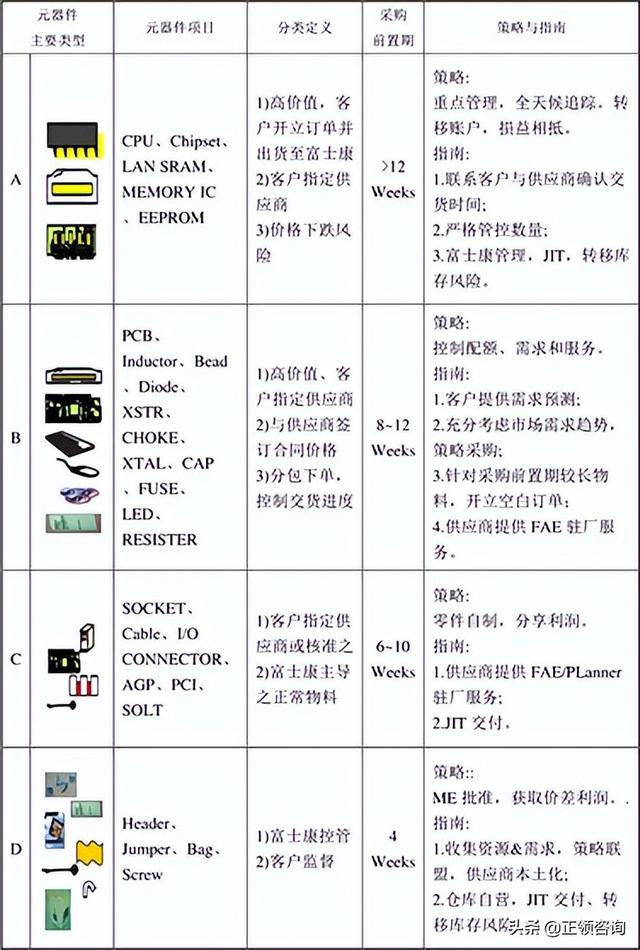
其中,由于B类物料主要是常规的的主/被动电子元器件,需要根据市场需求趋势,灵活变动策略来采购,主要采用VMI模式叫料。在该模式下,富士康各业务单元的采购人员定期向供应商提供空白订ౠ单,并每周更新物料需求,供应商根据富士康的物料需求提前备料及安排生产,按照最大需求量及最小需求量的要求补充出货至VMI-HUB(供应商在富士康园区设置的前置仓库),VMI-HUB原物料库存法定所有权归供应商,富士康各业务单元依实际生产计划领用物料,物料领用后物权发生转移。
VMI给富士康带来了什么
在引用VMI之前,富士康遵循的是传统的库存管理模式,重于对原物料的进、出、存的业务管理,目的是为了降低需求不确定性带来的风险。但因为传统模式信息共享机制的缺乏,信息失真导致的牛鞭效应的存在,富士康不得不保有大量原物料库存。随着公司业务版图的逐渐扩大,高保有量的原物料库存就像一座大山压在富士康身上,严重影响现金流,而此时,富士康作为全球3C产品代工制造的领军企业,外部环境又面临着全球市场的激烈争,富士康迫切需要引入一种创新的库存管理模式来增加自身竞争力。由此,在2000年7月,富士康引入VMI,在捷克建立了第一座VMI-HUB 𝕴后又在美国建立了多座VMI-HUB,借由海外VMI-HUB的成功的运营经验,2002年3月,富士康在深圳龙华园区建造了第一座国内的原物料𓂃VMI-HUB,也由此拉开了富士康全面实施原物料VMI库存管理的序幕。
富士康集团总裁郭台铭对VMI库存管理模式寄予厚望,他指示:VMI是策略优势并成为核心竞争力。富士康实施VMI遵从的原则是:要货有货,不要货时零库存;送料上线、用后付款;全球物料状况掌握;提供物料需求计划完🌊整清晰的物料信息。富士康对供应商VMI-HUB库存的目标性要求是:随时保持两周以上库存。而且富士康VMI-HUB建仓的策略是跟着产线走,哪里有制造哪里就有VMI-HUB,作为配套工程,在富士康南下北上扩张过程中,VIM库存管理几乎覆盖了所有重要客户的代工生产线。出于VMI供应商拥有库存的模式特点,富士康的原物料库存周转天数明显下降,原物料呆滞库存得到了有效遏制,缺料问题也得到缓解,生产📖顺畅了,产成品的交货率也提高了,可以说,VMI库存管理模式给富士康带来了实实在在的好处。
富士康的VMI给供应商带来了什么
随𒁃着对VMI运用的不断深入与供应链环境的变化,通过实施VMI获得巨大好处的同时也暴露了一些问题,细心的小伙伴可能已经觉察到了,富士康实行VMI获得的好处实际上是建立在广大供应商承担库存风险的基础上得来的。难道VMI库存管理模式就只是简单的将富士康身上的大山搬到了供应商身上?如果是这样的话,供应链整体库存压力问题并没有得到实际解决,这与该模式下降低供应链总成本的目标不符。实际上富士康的供应商对于运作VMI的积极性也不高,那这是VMI模式本身的缺陷还是富士康VMI实施的问题,我们来进一步🌠分析一下。
通过前文对VMI的描述,我们应该有这样的一个认识,在VMI的运行过程中,供应商与制造商应该是一种“策略联盟”的关系,大家信息共享,共同制定生产计划。制造商提供准确的生产预测,供应商主动承担库存风险,真正满足弹性生产,柔性管理需求,这应该是降低供需双方供应链成本的最理想状态。然💯而富士康处于供应链的核心节点,手握世界一流品牌客户资源,对于上游供应商而言,富士康是游戏规则的制定者,拥有绝对的话语权,地位的不对等,带来﷽的是供应商的绝对服从、妥协,是供应商承担额外的库存风险。
富士康的强势具体表现在以下几个方面:
(一)集中议价,最大限度压榨供应商利润
富士康设有中央集权的中央采购部门,专职负责集团物料的全球采购工作,策略是捆绑集团所有业务单元的物料需求与供应商进行集中采购谈判,定期(通常为每年各季度节点)召集全球供应商进行现场或视频会议,洽谈涵盖询价、议价等在内的采购相关事宜。会议结束后采购价格会被整理成价格库,供各业务单元遵照执行。统一窗口、集中议价,极大的强化了富士康的议价权。在电子元器件的同质化现象越来越严重的当前,海量的供应商遍布全球,多头竞争的现象日益加剧,富士康采用价格驱动的采购决策体系再加๊上中央采购的内部考核指标,使得富士康中央采购会竭尽全力对供应商进行压价、比价,最大程度的压榨供应商报价以获取利润空间,供应商为了维系客源、避免市场流失,往往选择以价换量的销售策略。
(二)以服务富士康为第一要务
VMI框架协议由富士康拟定,协议包括:货物保全、交付、权责、保密协议🅺等20多项条款,VMI-HUB为供应商提供有偿服务,供应商为了配合执行VMI则必须要支付仓储费用、物流费用与意外损失等。富士康“要货有货,不要货时零库存”的原则决定了在任何时候,供应商应以满足富士康的需求为第一要务。
(三)在牛鞭效应依然存在的情况下,供应商承担主要库存风险
富士康现行的需求预测周期是13周,一是下游客户端给富士康报的需求是13周,二是为了配合13周刚好一个季度的议价节点。然而受原材料、市场需求、生产工艺等因素影响,目前大部分参与实施VMI的供应商当中,被动电子元器件的采购前置器均小于13周,少部分前置时间长的物料会大于13周,也就是说,前置时间短的物料供应商实际的备货将会大于预测需求,前置时间长的物料供应商的备货将会少于预测需求,存在库存积压𝓡或缺货的风险,且预测周期较长,下游客户端需求波动几率大。
富士康各业务单元的KPI是每年春节放假之前,主管与下属一起,对不同职位制定来年工作目标,到年终时,再就个人的工作业绩参照设定的工作目标进行年度总体考评,考虑到自身利益最大化,各业🍷务单元所设定的目标可能会与供应链整体目标发生矛盾。为了争取资源,完成任务,达成客💎户满意度,不希望受到供应不足的困扰,个业务单元会报出更高的物料预测,以确保有充足的供应。
VMI运行的前提是供需各方信息互通,需求预测准确💛,供应商对于库存的把握精准,在此前提下,理论上,供应商主动承担的库存风险不大。然而,供应链是一个复杂的系统,充满着各种不确定因素,这些因素潜藏着多重风险,最大的不确定性因素就来自客户端需求波动,富士康现行的规则又存在局限性,再加上牛鞭效应导致的需求预测失真,都将使供应商面临库存积压或缺货的风险。库存积压意味着资金占用,缺货意味着高额罚款或补货成本,在实体经济不景气的当前,对供应商而言,很可能成为压死其的最后一根稻草。
(四)在供应商承担主要库存风险的同时未设置有效的激励措施
供应链贯穿从供应商到终端客户的整个过程,完整的供应链离不开供应商,没有激励措施就无法保证供应商物料的优质与稳定,对供应商的绩效进行客观、公正、科学的评价是制造商对供应商实施激励措施的前提。完善的供应商绩效评估体系应该是根据供应商的绩效表现进行分类管理、区别对待,管理上做到奖惩结合。富士康目前对参与VMI供应商的考核主要是通过供应商记分卡系统实现:根据得分结果进行分级处理,不合格的供应商或将通过整改重🐟新纳入亦或被取消供应商资格。该评估体系侧重于对供应商的审核、监督与惩罚,在将库存风险转嫁供应商的情况下并未设置对供应商的激励措施,光让牛干活,也不见给牛吃草。
总结
看到这里,我们也大概清楚了,VMI模式本身是有极高的精细化管理能力的,但在实务中却有些不对味,归根结底还是因为角色的地位不对等。对于供应商而言,尽管富士康利用强势地位不断压榨其利润,且需自行承担主要的库存风险,但因富士康电子元器件需求稳定且集中,供应商需要♉依赖富士康从全球市场上获取源源不断的生意机会和预期,所以,有些变异的VMI依旧火爆。但大浪淘沙,对供应商而言,正如一场豪赌:短期看,其可以靠批量和规模在有限的利润空间内求得生存空间;长远看,稳定且持续的业务有助其自身的成长,或许哪一天就可以平等对话,落实VMI的合作共赢目标也不是不可能。
小伙伴们,本期分享到此结束。为何富士康仓库“白骨累累”,您有答案了么?
好了,这篇文章的内容发货联盟就和大家分享到这里,如果大家网络推广引流创业感兴趣,可以添加微信:80709525 备注:发货联盟引流学习; 我拉你进直播课程学习群,每周135晚上都是有实战干货的推广引流技术课程免费分享!